- Mobile: 0086-13083991987
- E-mail: market@micmachinery.com
- Shipment: exporting country
- Customer reviews: click on
Introduction:
In the realm of pharmaceutical ingenuity, Eye Drop Filling Machine Manufacturers stand at the forefront of precision and innovation, crafting technological marvels that define the landscape of ophthalmic product manufacturing. These manufacturers play a pivotal role in the pharmaceutical industry, providing state-of-the-art solutions that meet the exacting demands of eye care products. As we delve into the distinctive product characteristics, diverse applications, and the intricate mechanical principles employed by these manufacturers, we embark on a journey to explore the essence of excellence in eye drop filling. From sterile formulations to specialized medications, these machines ensure each dropper is filled with the utmost accuracy, consistency, and the promise of promoting optimal eye health.
Product Characteristics:
Eye Drop Filling Machine Manufacturers pride themselves on engineering machines with exceptional characteristics, meticulously designed for precision and compliance. Crafted from materials adhering to stringent pharmaceutical standards, these machines ensure durability while upholding the highest standards of quality and hygiene. Automated vial or dropper feeding, precise filling, and sealing mechanisms are the hallmarks of their creations, striking a delicate balance between automation and the intricacies of pharmaceutical manufacturing. These machines feature user-friendly interfaces with adjustable controls, accommodating various dropper sizes and formulations. Equipped with anti-contamination features and sterile sealing capabilities, products from these manufacturers preserve the integrity of eye drop formulations, delivering solutions that resonate with both quality and the promise of optimal eye care.
Product Applications:
The offerings of Eye Drop Filling Machine Manufacturers span the entire spectrum of ophthalmic product manufacturing, providing comprehensive solutions for efficient and precise filling and sealing of dropper bottles. Whether producing standard lubricating eye drops or specialized medications for glaucoma or infections, these machines ensure uniformity in dosage and presentation. The versatility of products from these manufacturers caters to the dynamic requirements of the pharmaceutical industry, where each eye care product necessitates a tailored approach to dispensing, capping, and preserving its unique formula.
Mechanical Principle:
At the core of the solutions provided by Eye Drop Filling Machine Manufacturers lies advanced mechanical principles designed for delicacy, speed, and compliance. These machines utilize dropper feeding systems, dosing pumps, and filling nozzles to accurately measure and dispense the specified quantity of eye drop solution into individual dropper bottles. Sealing mechanisms, often employing high-speed technology and cleanroom conditions, secure the bottles, preserving the sterility and effectiveness of the eye drops. Integrated sensors and programmable logic controllers (PLCs) oversee the entire process, ensuring uniformity, minimizing errors, and enhancing the overall efficiency of eye drop filling operations.
In conclusion, Eye Drop Filling Machine Manufacturers stand as architects of precision in the pharmaceutical industry. Their exceptional product characteristics, diverse applications, and commitment to advanced mechanical principles make them indispensable partners for pharmaceutical companies globally. By embracing cutting-edge technology, these manufacturers not only ensure the accuracy of eye drop filling but also uphold the highest standards of presentation, consistency, and quality. As fundamental contributors to ophthalmic product manufacturing, they continue to shape the way eye care products are filled, ensuring each dropper embodies the essence of precision and the promise of enhanced eye health.
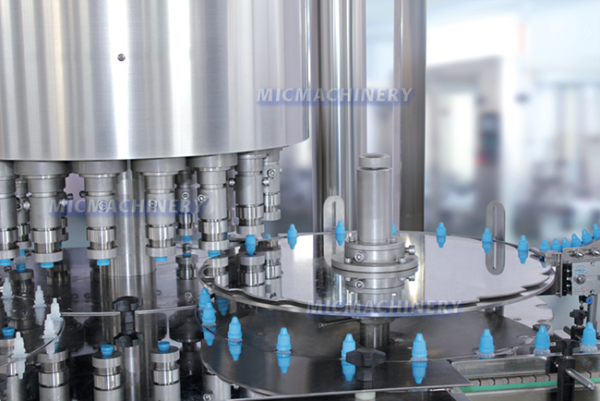
Plastic cap screwing system
The motor transmits the power to the main shaft through the transmission device, so that the turntable rotates. Because the central gear does not rotate, the rotary cap rotates because of the rotation of the gear of the rotary cap shaft. The machine will automatically grab the cap, and the bottle will automatically screw the cap when it reaches the specified position,no bottle then no cover, when the rotation of the cap side moving down, rotation (pressure) cap under the action of the CAM to complete cover. Then by the drawing wheel into bottle delivery.
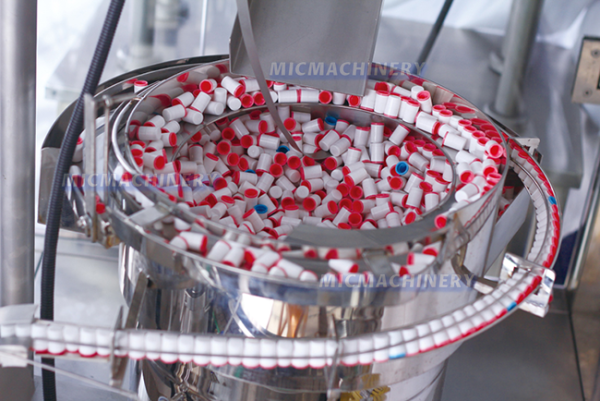
cover loading automatically
Cover feeding cage with vibrating disk is connected to a pipe that carries the outside cover ,They automatically arranges the outside cover and deliver the outside cover.
In this way, the small bottle is covered in a Coherent process, reducing the manual contact with the syringe process, and ensuring bottle hygiene,At the same time, labor costs are reduced.
*Automatic bottle handling system
*Conveying bottle, removing bottle pouring system
*Static elimination, air washing bottle system (optional)
*Static electricity elimination, gas washing plug cap system
*Precision ceramics, filling and bottle dividing system (optional)
*Vacuum plug system
*Grab and cover system
*Constant magnetic torque, positioning and capping system
*100 level laminar flow protection aseptic system
Basic performance characteristics
1. Touch screen operation platform
2. Host frequency control, automatically display the current working frequency
3. The filling volume can be adjusted as a whole or fine-tuning
4. No bottle, no filling
5. If there is no bottle, there is no plug
6. No inner plug, no outer cover
7. The capping station is equipped with bottle clamping device and top cover device
eight Stop the machine when there is no bottle and start automatically when there is bottle nine When the rotary table clamps the bottle, the torque limiting device can stop the machine for protection
ten Equipped with a 60L liquid storage tank, two proximity switches on and off the floating ball in the liquid storage tank + angle valve control for automatic material replenishment (the liquid replenishment system of the liquid storage tank needs to be in the state of liquid replenishment when the main engine power is turned on, and after the power is turned off, the liquid replenishment system needs to be in the state of closed no matter how much the liquid level is)
In short, we will try our best to provide you with satisfactory service,the following is our customer feedback:
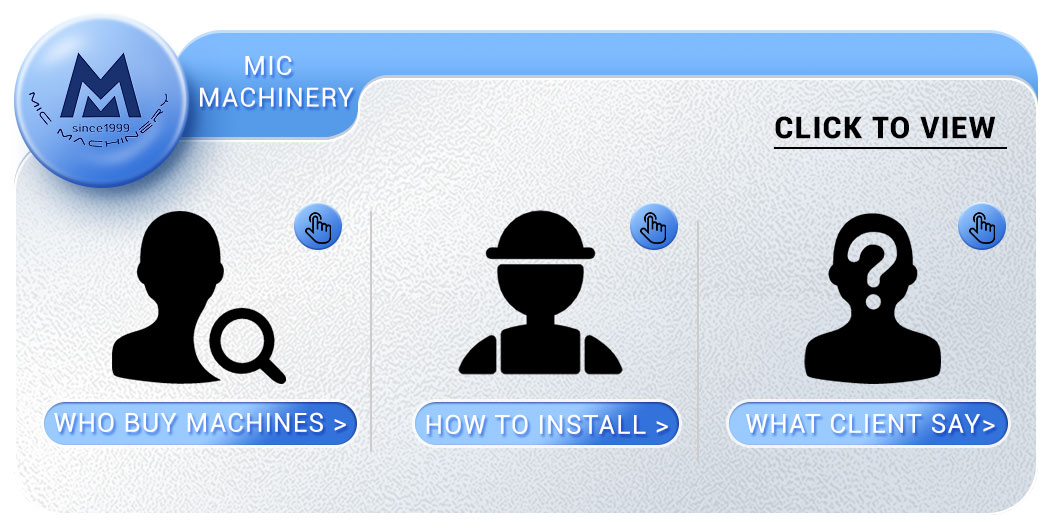