φ25mm-38mm Tube Manufacturing Machine
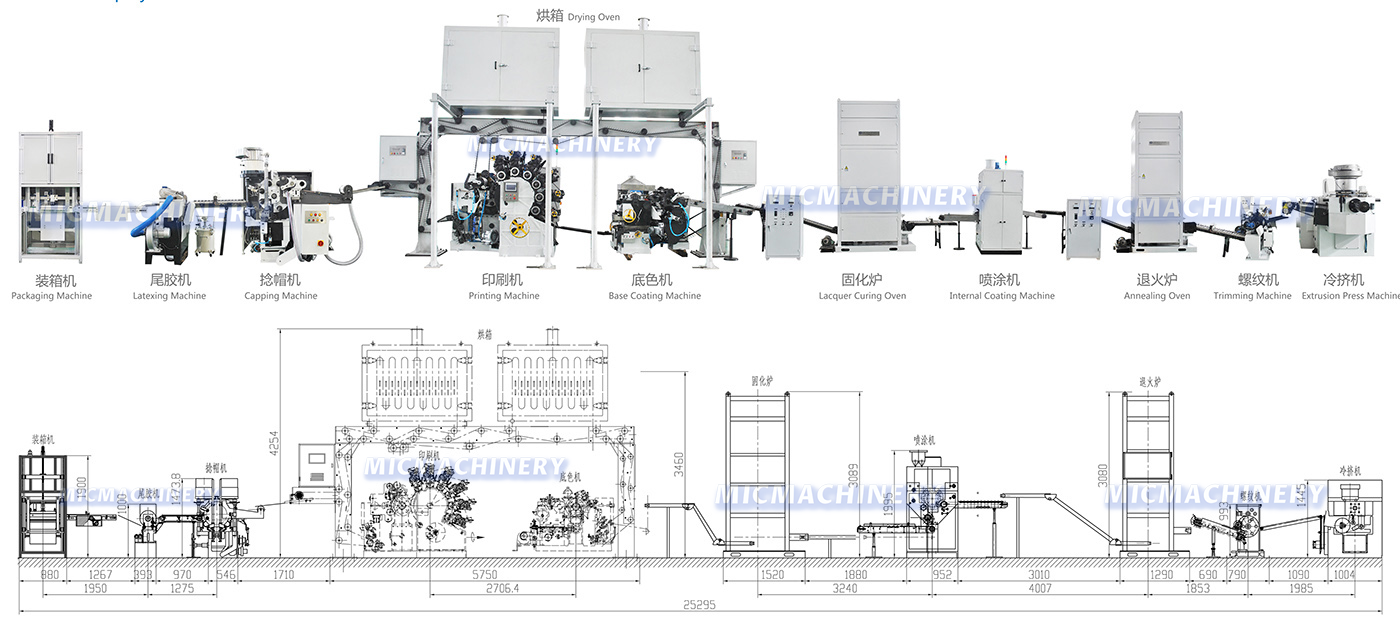
Tube Making Line Video
Tube Making Line All Machines
Title: Unveiling Tube Making Machines: Understanding Price, Manufacturing, and Workflow
In the realm of industrial manufacturing, tube making machines play a pivotal role in producing high-quality tubes used across diverse applications. From construction projects to automotive components, these machines are essential for shaping raw materials into precise tubes of varying sizes and specifications. In this article, we delve into the intricate aspects of tube making machines, focusing on their pricing, manufacturing capabilities, and workflow dynamics.
Tube Making Machine Price:
2. Production Capacity: Machines with higher production capacities typically command a higher price due to their ability to handle larger volumes of raw materials and output a greater number of finished tubes within a given timeframe.
3. Quality and Durability: The quality of materials used in manufacturing the machine, as well as the reputation of the manufacturer, can impact its price. High-quality machines built to withstand heavy-duty usage and offer longevity often come with a higher initial investment.
4. Additional Features and Customization: Some tube making machines may offer additional features or customization options to cater to specific production requirements. These added functionalities can contribute to an increase in the overall price of the machine.
Tube Manufacturing Machine Usage:
Tube making machines find application across various industries, serving as indispensable tools in the production of tubes for a wide range of purposes:
1. Construction: In the construction industry, tube making machines are utilized to produce structural tubes used in building frameworks, scaffolding, and architectural designs. These machines ensure precision and consistency in tube dimensions, contributing to the structural integrity of construction projects.
2. Automotive: Tube making machines play a crucial role in the automotive sector, where tubes are used in exhaust systems, chassis components, and fluid transfer systems. These machines enable the production of tubes with precise specifications, meeting the stringent quality standards required in the automotive industry.
3. Manufacturing: Across manufacturing sectors, tube making machines are instrumental in producing tubes used in machinery, equipment, and industrial applications. These machines facilitate the fabrication of tubes with customized shapes, dimensions, and materials to suit specific manufacturing requirements.
Tube Making Line Workflow:
The workflow of a tube making machine encompasses various stages, each contributing to the seamless production of high-quality tubes:
1. Material Feeding: The process begins with the feeding of raw materials, such as metal coils or sheets, into the machine. Depending on the type of machine, the material may undergo shaping, forming, or welding processes to initiate the tube manufacturing process.
2. Shaping and Forming: Tube making machines employ various techniques, including roll forming, welding, or extrusion, to shape the raw material into the desired tube profile. Advanced technologies and precision controls ensure accuracy and consistency in tube dimensions throughout the shaping process.
3. Finishing and Quality Control: Once the tube is formed, it undergoes finishing processes such as cutting, sizing, and surface treatment to achieve the desired specifications and quality standards. Quality control measures are implemented to inspect and verify the integrity of the finished tubes before they are deemed ready for use.
In conclusion, tube making machines play a crucial role in the manufacturing industry, enabling the efficient production of high-quality tubes for diverse applications. By understanding the pricing factors, applications, and workflow dynamics of these machines, businesses can make informed decisions regarding their investment in tube manufacturing technology, thereby enhancing productivity and competitiveness in the market.
In the realm of industrial manufacturing, tube making machines play a pivotal role in producing high-quality tubes used across diverse applications. From construction projects to automotive components, these machines are essential for shaping raw materials into precise tubes of varying sizes and specifications. In this article, we delve into the intricate aspects of tube making machines, focusing on their pricing, manufacturing capabilities, and workflow dynamics.
Tube Making Machine Price:
When considering investing in a tube making machine, understanding the pricing dynamics is paramount. The price of these machines can vary based on several factors:
1. Machine Type and Complexity: Tube making machines come in various types, including roll forming machines, welding machines, and extrusion lines. The complexity of the machine, along with its technological features and automation capabilities, can significantly influence its price.2. Production Capacity: Machines with higher production capacities typically command a higher price due to their ability to handle larger volumes of raw materials and output a greater number of finished tubes within a given timeframe.
3. Quality and Durability: The quality of materials used in manufacturing the machine, as well as the reputation of the manufacturer, can impact its price. High-quality machines built to withstand heavy-duty usage and offer longevity often come with a higher initial investment.
4. Additional Features and Customization: Some tube making machines may offer additional features or customization options to cater to specific production requirements. These added functionalities can contribute to an increase in the overall price of the machine.
Tube Manufacturing Machine Usage:
Tube making machines find application across various industries, serving as indispensable tools in the production of tubes for a wide range of purposes:
1. Construction: In the construction industry, tube making machines are utilized to produce structural tubes used in building frameworks, scaffolding, and architectural designs. These machines ensure precision and consistency in tube dimensions, contributing to the structural integrity of construction projects.
2. Automotive: Tube making machines play a crucial role in the automotive sector, where tubes are used in exhaust systems, chassis components, and fluid transfer systems. These machines enable the production of tubes with precise specifications, meeting the stringent quality standards required in the automotive industry.
3. Manufacturing: Across manufacturing sectors, tube making machines are instrumental in producing tubes used in machinery, equipment, and industrial applications. These machines facilitate the fabrication of tubes with customized shapes, dimensions, and materials to suit specific manufacturing requirements.
Tube Making Line Workflow:
The workflow of a tube making machine encompasses various stages, each contributing to the seamless production of high-quality tubes:
1. Material Feeding: The process begins with the feeding of raw materials, such as metal coils or sheets, into the machine. Depending on the type of machine, the material may undergo shaping, forming, or welding processes to initiate the tube manufacturing process.
2. Shaping and Forming: Tube making machines employ various techniques, including roll forming, welding, or extrusion, to shape the raw material into the desired tube profile. Advanced technologies and precision controls ensure accuracy and consistency in tube dimensions throughout the shaping process.
3. Finishing and Quality Control: Once the tube is formed, it undergoes finishing processes such as cutting, sizing, and surface treatment to achieve the desired specifications and quality standards. Quality control measures are implemented to inspect and verify the integrity of the finished tubes before they are deemed ready for use.
In conclusion, tube making machines play a crucial role in the manufacturing industry, enabling the efficient production of high-quality tubes for diverse applications. By understanding the pricing factors, applications, and workflow dynamics of these machines, businesses can make informed decisions regarding their investment in tube manufacturing technology, thereby enhancing productivity and competitiveness in the market.
Application
- Hot Sauce Filling Production Line
- Lube Oil Production Line
- Olive Oil Production Line
- Perfume Production Line
- Silicone Production Line
- Beer Production Line
- Tube Manufacturing Machine
- Filling Machine Manufacturer
- Visual Inspection Machine
- Bottle Blowing Machine
- Laser Coding Machine
- Aseptic Cold Filling Machine
- Fruit and Vegetable Processing Machinery Manufacturer
- Dairy Products Machinery
- Alcoholic Drink Production Equipment
- Commercial Water Treatment System
- Blowing Filling Capping Machine
- Barrel Filling Line