Guide to Picking the Best Bottle Filling & Capping Machine
Selecting the right bottle filling machine and bottle capping machine is more than a purchase—it’s a decision that shapes your production efficiency, product quality, and bottom line. The wrong choices lead to bottlenecks, waste, and frustrated teams, while the right ones turn your line into a smooth, scalable operation. We will explain in detail how to select these machines, address common pain points, and provide feasible solutions.
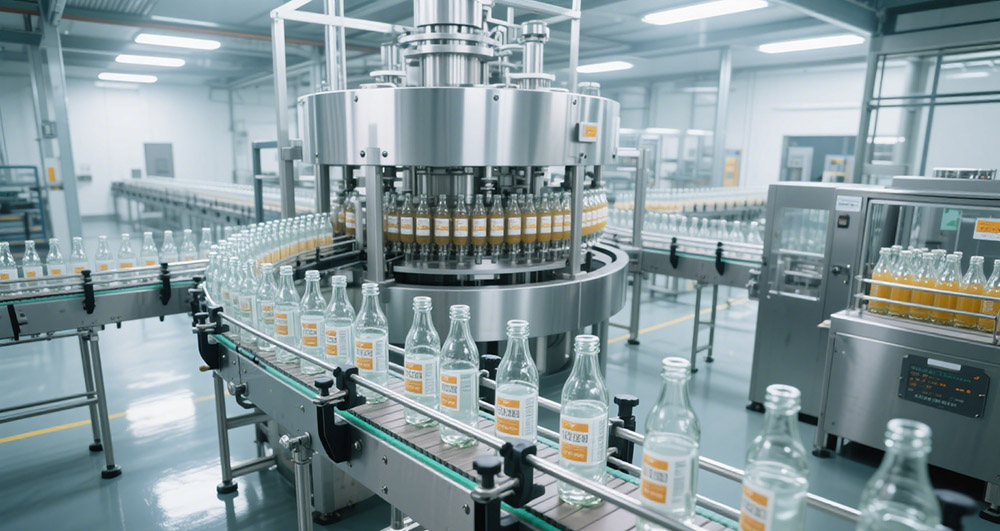
Start with Production Scale: Matching Machines to Your Output Needs
One of the biggest mistakes businesses make is investing in a bottle filling machine or bottle capping machine that’s too big or too small for their output. A high-speed automatic machine for a small bakery filling 100 jars/day wastes energy and money, while a manual filler for a beverage plant churning out 5,000 bottles/day creates endless delays.
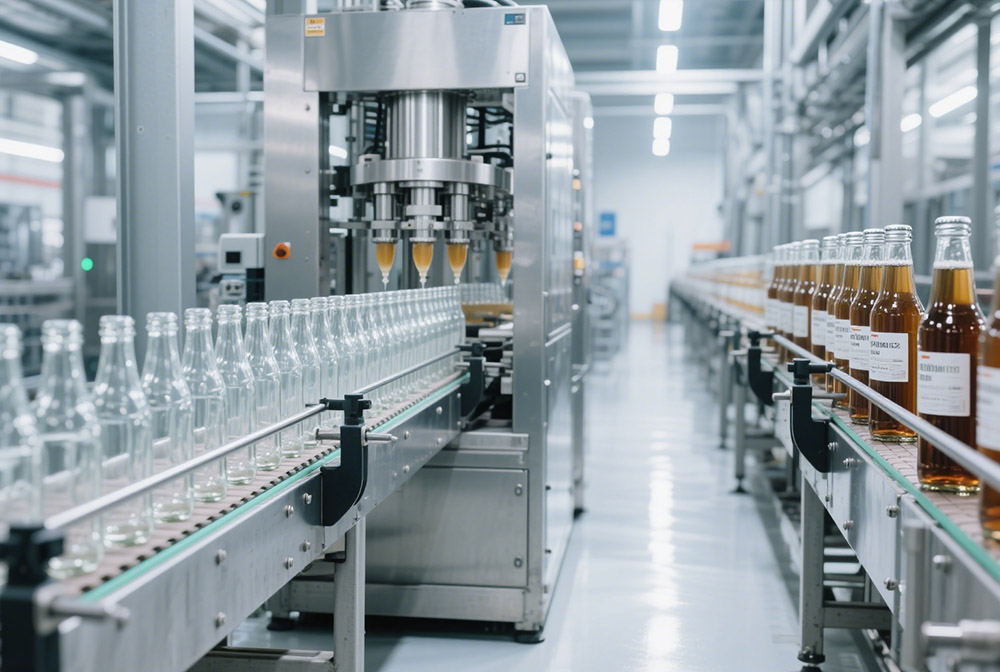
For large-scale operations (500+ bottles/hour), automatic systems are non-negotiable. An automatic bottle filling machine with PLC controls and multiple nozzles ensures consistent fills, even with 6,000 bottles/hour. Pair it with an automatic bottle capping machine that syncs speeds, using sensors to align caps perfectly—critical for meeting tight deadlines in industries like soft drinks or cosmetics.
Medium operations (100–500 bottles/hour) thrive with semi-automatic setups. A semi-auto bottle filling machine lets operators load bottles while it handles precise filling, cutting human error. A semi-auto bottle capping machine takes over sealing, reducing fatigue from manual twisting. This balance keeps costs low without sacrificing speed.
Small batches (under 100 bottles/hour) benefit from manual or tabletop machines. A compact bottle filling machine with hand-operated levers works for artisanal sauces or craft beers, while a portable bottle capping machine ensures consistent seals without taking up too much space.
Always calculate your peak demand, not just averages. If your busiest days hit 300 bottles/hour, choose a machine that handles 350–400 to avoid bottlenecks. Seasonal businesses should opt for adjustable-speed models to scale up or down as needed.
Prioritize Material Compatibility: Protecting Bottles and Products
Bottles and products have unique needs—PET vs. glass, thick vs. thin liquids—and using the wrong machine leads to damaged goods. A one-size-fits-all approach wastes money on broken glass, warped plastic, or uneven fills.
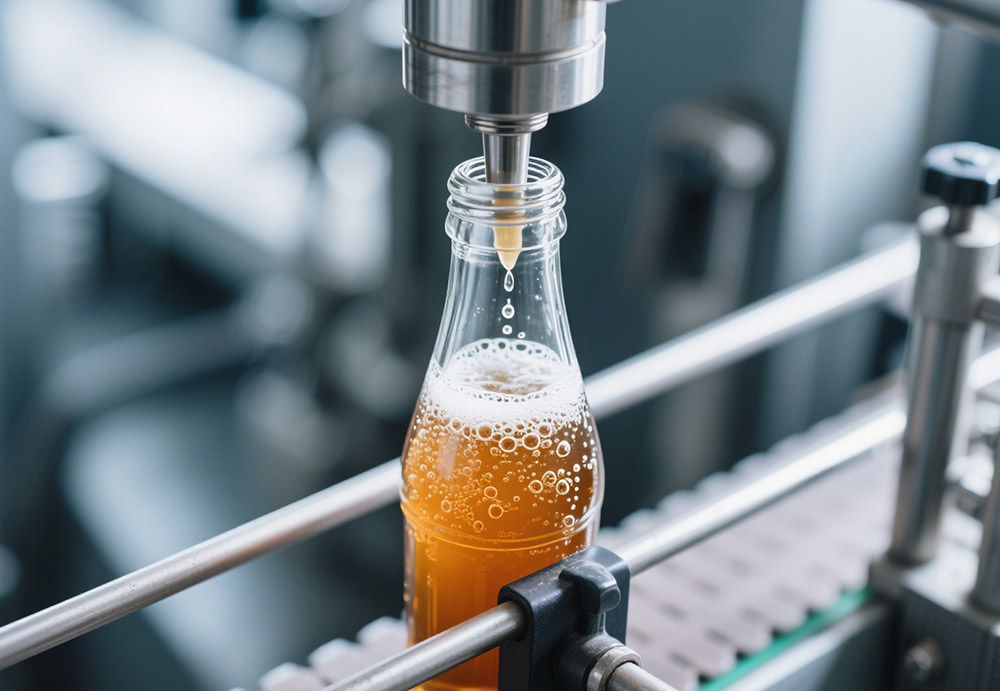
PET bottles require gentle handling. A PET bottle filling machine with soft-grip conveyors and pressure-sensitive nozzles prevents deformation, even with lightweight plastic. Pair it with a PET bottle capping machine that applies gradual torque to avoid crushing the neck—essential for carbonated drinks, where pressure can cause leaks if seals are uneven.
Glass bottles demand precision. A glass bottle filling machine uses slow-moving parts and shock-absorbent belts to prevent shattering, a must for wines, spirits, or pharmaceutical vials where breakage ruins inventory. A glass bottle capping machine adjusts clamping force to protect fragile edges, ensuring caps seal tight without cracking the glass.
Product viscosity matters too. Thick liquids like honey or lotion need a bottle filling machine with wide, heated nozzles to prevent clogs, while thin liquids such as water or perfume require anti-drip technology to avoid waste. Mismatched equipment here leads to inconsistent fills—some bottles overflow, others underfill—damaging customer trust. Test machines with your actual product to avoid surprises.
Ensure Speed and Sync: Making Filling and Capping Work in Tandem
Even top-tier individual machines fail if they don’t work together. A bottle filling machine that outpaces the capper creates backups, spilling product and slowing the line. Conversely, a slow filler leaves the capper idle, wasting energy.
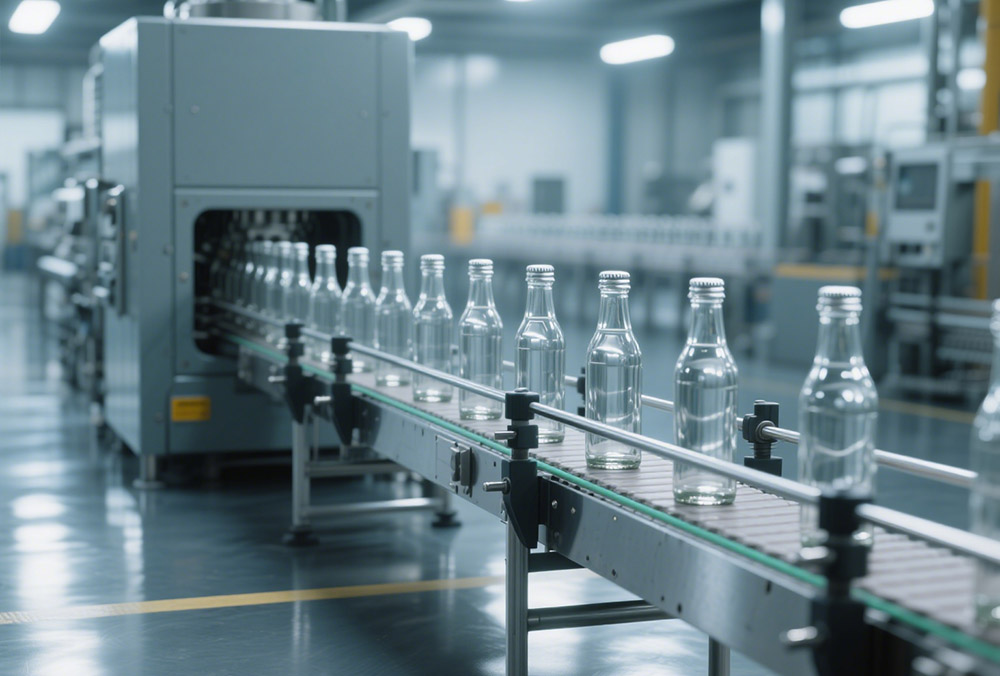
Start by matching speeds. If your bottle filling machine outputs 200 bottles/hour, your bottle capping machine must hit the same rate. Automatic models solve this with synchronized PLC systems that adjust in real time—if the filler speeds up, the capper follows. For semi-automatic setups, train operators to monitor flow, pausing the filler briefly if the capper falls behind.
Bottle size consistency is key. A machine that handles 500ml round bottles may struggle with 100ml square ones, throwing off sync. Look for adjustable guides and quick-change parts that adapt to your bottle range. For example, a bottle filling machine with adjustable nozzle height or a bottle capping machine with interchangeable cap chucks lets you switch sizes in minutes, not hours.
Test integration before buying. Many manufacturers offer demos with your actual bottles, revealing issues like misaligned caps or spilled liquid that only appear in real-world use. This step saves you from costly returns or retrofits later.
Factor in Maintenance and Durability: Reducing Downtime
A machine that breaks down weekly is worse than no machine at all. The best bottle filling and capping machines balance performance with easy upkeep, minimizing downtime.
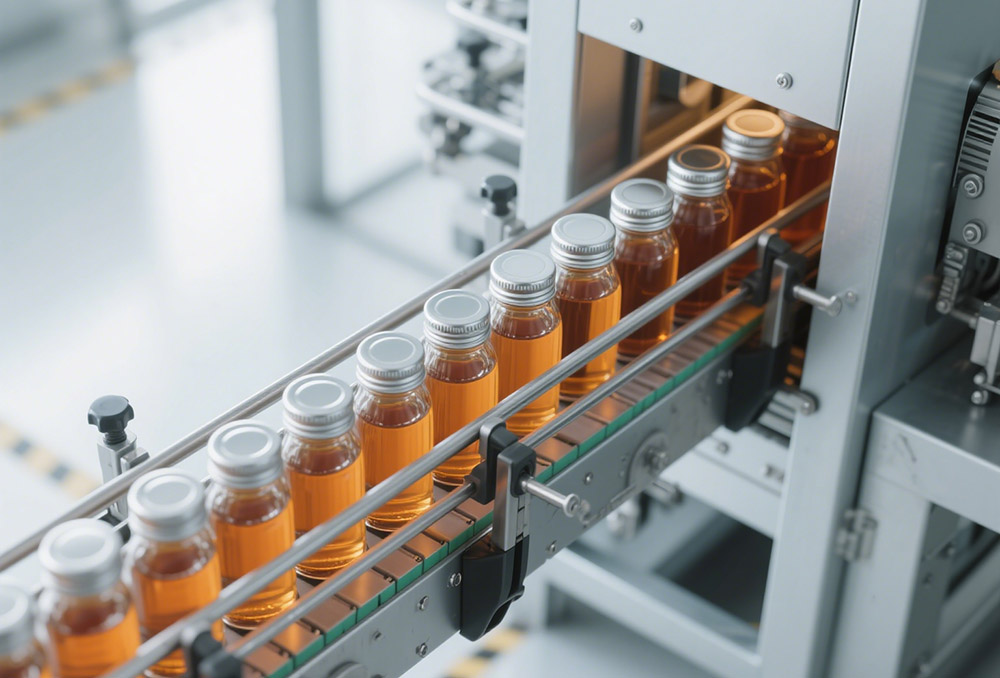
Look for a bottle filling machine with modular design—nozzles, pumps, and conveyors that detach quickly for cleaning or repairs. Stainless steel parts resist corrosion, critical for food or pharmaceutical lines, and clear user manuals with troubleshooting guides help your team fix small issues fast.
For bottle capping machines, prioritize simplicity. Models with tool-free torque adjustments or easy-to-replace gears reduce repair time. Automatic versions with self-diagnostic lights flag problems (e.g., “low cap supply” or “misalignment”) before they halt production, while semi-autos have fewer moving parts to fail.
Check for local support. A machine with a manufacturer’s service center nearby or online parts catalogs ensures you’re not waiting weeks for replacements. Warranties matter too—aim for 1–3 years of coverage to protect your investment.
Plan for Growth: Scalable Machines That Adapt to Your Business
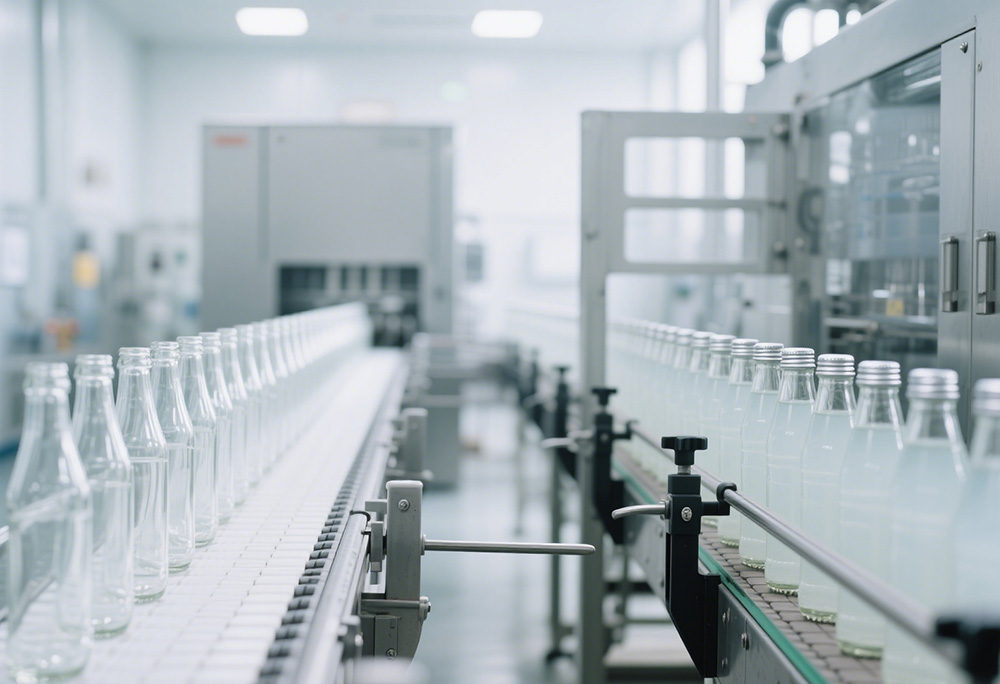
Today’s perfect machine may be obsolete in two years if your business grows. Choose equipment that scales with you, avoiding costly upgrades.
A semi-auto bottle filling machine that converts to automatic with add-on nozzles or a conveyor system grows with your output. Similarly, a bottle capping machine with adjustable speed controls lets you boost production as demand rises. For tight spaces, consider an all-in-one bottle filling and capping machine—compact now, but ready to add labeling or packaging modules later.
Ask about future compatibility. Can the bottle filling machine handle larger bottles if you expand your line? Will the bottle capping machine work with new cap styles, like child-resistant lids for a pharmaceutical line? Flexibility here saves tens of thousands in replacement costs down the road.
Small businesses should avoid overcommitting. Start with a semi-auto setup that fits your current needs, but check that it accepts upgrades (e.g., a foot pedal for hands-free operation or extra nozzles for faster filling) as you grow.
Choosing the best bottle filling machine and bottle capping machine requires balancing your production scale, material needs, and growth goals. By addressing output matching, material compatibility, integration, maintenance, and scalability, you’ll build a line that runs smoothly, reduces waste, and adapts as your business evolves. Remember: the right equipment isn’t just a tool—it’s a partner in your success.