- Mobile: 0086-13083991987
- E-mail: market@micmachinery.com
- Shipment: exporting country
- Customer reviews: click on
Main structure description:
The silicone color mixing machine is divided into a geared motor, a cover, a planet carrier, a mixer, a wall scraper, a bucket, a single-column hydraulic lifting system, a vacuum system, and a frame. It is a new and high-efficiency mixing device developed by innovation and improvement on the basis of digesting and absorbing advanced technologies at home and abroad.
Working principle :
When the planet carrier rotates, it drives the three stirring and dispersing shafts in the box to revolve around the axis of the barrel while rotating at high speed, so that the material is subjected to strong shearing and kneading to achieve the purpose of full dispersion and mixing; there is a scraper on the planet carrier The wall knife rotates with the planet carrier, and it is continuously scraped against the wall of the barrel to make the wall of the barrel free of retained materials and improve the mixing effect. The length of the mixing time is controlled by the user according to the properties of the material and can be adjusted through the control panel. The cover and planetary mixer are hydraulically lifted and lowered by a single column, and the operation is flat and hidden, fast and light.
This device can work under vacuum and can continuously discharge water and other volatiles. Therefore, it can be used as a degassing kettle. The barrel can be heated or cooled by oil and water circulation as required; steam heating can also be used. The heating temperature is displayed by the temperature controller on the control panel.
Because this device has good mixing, shearing and dispersing effects, it is especially suitable for solid-solid, solid-liquid, and liquid-liquid dispersion and mixing, so it is used in chemical, food, light industry, pharmaceutical, building materials and other industries Both can be widely used.
In the field of pharmaceutical engineering, precise and efficient mixing is a fundamental process for the production of high-quality pharmaceutical products. Planetary mixers have emerged as indispensable tools, offering advanced mixing capabilities that cater specifically to the needs of pharmaceutical engineering. In this technical introduction, we explore the diverse applications and benefits of silicone color mixing machine, highlighting their pivotal role in optimizing manufacturing processes and achieving superior product quality.
silicone color mixing machine are renowned for their precise and consistent mixing results, making them a preferred choice in pharmaceutical engineering. These mixers employ a unique mixing action that combines rotation and revolution, facilitating thorough blending of ingredients. The planetary motion of the mixing arm, rotating on its own axis while simultaneously orbiting around the mixing vessel, ensures effective distribution of materials and promotes optimal homogeneity of pharmaceutical formulations. This precision is critical for achieving uniform distribution of active ingredients and other components.
One of the primary advantages of silicone mixer is their versatility in handling a wide range of pharmaceutical formulations and processes. These mixers can accommodate various viscosities, consistencies, and volumes, making them suitable for applications such as blending powders, granulation, wet and dry mixing, emulsification, and dispersing solid dosage forms. Whether it involves tablet compression, capsule filling, or the production of creams and ointments, planetary mixers offer the flexibility required in pharmaceutical engineering processes.
Efficiency and productivity are essential factors in pharmaceutical engineering. silicone mixing machine offer efficient mixing capabilities, reducing the overall processing time required for blending pharmaceutical ingredients. The combination of planetary motion, powerful motors, and purpose-designed mixing tools ensures rapid and thorough mixing, resulting in improved production efficiency and increased throughput. This time-saving advantage enables pharmaceutical engineers to optimize their manufacturing processes and meet demanding production schedules.
Pharmaceutical engineering operates within stringent regulatory frameworks and adheres to high-quality standards, including Good Manufacturing Practices (GMP). Planetary mixers are designed to meet these exacting requirements, providing features that ensure compliance and enhance quality assurance. Features such as sanitary designs, easy-to-clean surfaces, and sealed mixing vessels facilitate thorough cleaning, prevent cross-contamination, and promote product safety. Additionally, advanced control systems enable precise monitoring and adjustment of mixing parameters, ensuring consistent quality throughout the pharmaceutical engineering process.
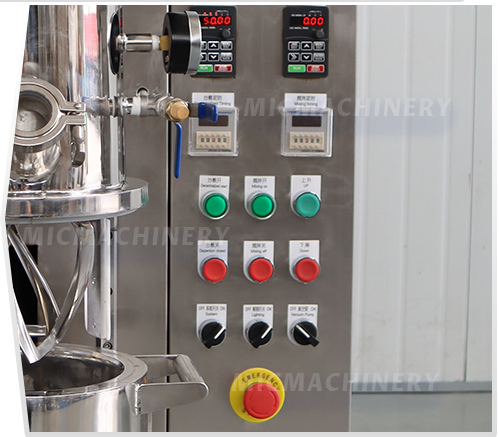
Control Panel
Use the control panel to control the switch of the machine
The heating temperature is displayed by the temperature controller on the control panel.
The length of mixing time is controlled by the user according to the different properties of the material and can be adjusted by the control panel
Double Planetary Mixer Stirrer
When the planetary frame rotates, it drives the three stirring in the box, and the dispersion axis rotates around the barrel axis at the same time, so that the material is subject to strong shear and kneading effect, so as to achieve the purpose of full dispersion and mixing; There is a wall scraper on the planetary rack rotating with the planetary rack, close to the barrel wall continuous scraping, so that the barrel wall without retained material, improve the mixing effect
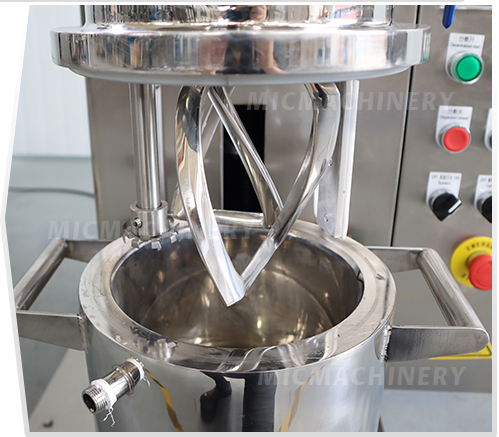
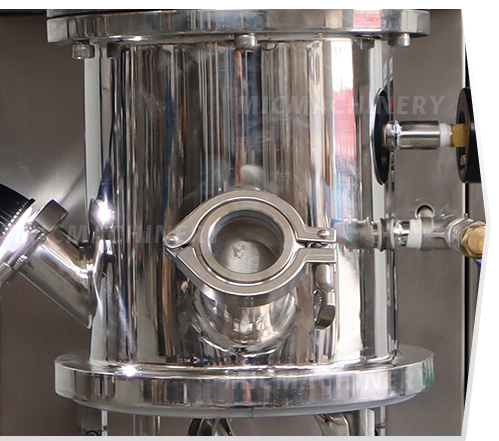
Double Panetary Mixer Charging Basket
This device can work under vacuum and can continuously discharge water and other volatiles. Therefore, it can be used as a degassing kettle. The barrel can be heated or cooled by oil and water circulation as required; steam heating can also be used. The heating temperature is displayed by the temperature controller on the control panel.
Because this device has good mixing, shearing and dispersing effects, it is especially suitable for solid-solid, solid-liquid, and liquid-liquid dispersion and mixing, so it is used in chemical, food, light industry, pharmaceutical, building materials and other industries Both can be widely used.
In short, we will try our best to provide you with satisfactory service,the following is our customer feedback.
Item |
Parameter |
Voltage |
380 V 50 Hz (3 phases) |
Tank design volume |
60 L |
Tank work volume |
50 L |
Mixer motor power |
4Kw |
Dispenser motor power |
5.5KW |
Revolution speed |
0~65 rpm Adjustable |
Mixing rotary speed |
0~100 rpm Adjustable |
Scraper speed |
0~65 rpm Adjustable |
Dispenser rotary speed |
1450rpm Adjustable |
Vacuum degree |
- 0.09 Mpa |
Hydraulic Lifting stroke |
600 mm |
Hydraulic Lifting power |
0.75Kw |
Vacuum |
Reserve vacuum interface with 370KW oil ring vacuum pump |
Dimension |
Host:1860x800x1970mm
|
Frequency Changer | Easydrive (Shenzhen) |
Motor | Kiper (Wuxi) |
Reduction Gears | Jiahe (Zhejiang) |
Vacuum Pump | Tingwei (Zhejiang) |
Hydraulic Station | Guang Deyang (Wuxi) |
304 Stainless Steel | Tisco (Tianjing) |
Main Electrical Components | Chint (Zhejiang) |