- Mobile: 0086-13083991987
- E-mail: market@micmachinery.com
- Shipment: exporting country
- Customer reviews: click on
Technical Introduction to Weight Detector Systems: Enhancing Precision in Quality Control
In today's fast-paced manufacturing environment, the need for accuracy and reliability in production lines has never been more crucial. Weight detectors are essential tools that play a significant role in ensuring product quality and consistency, particularly in industries such as food processing, pharmaceuticals, packaging, and more. These devices are designed to automatically measure the weight of products, checking for underweight or overweight items in real-time, ensuring that every product meets the required specifications.
A weight detector is commonly integrated into automated production lines to streamline the quality control process. These systems utilize highly sensitive sensors and advanced algorithms to detect any weight discrepancies with remarkable precision. By identifying deviations in product weight, the system helps to prevent product waste, minimize errors, and maintain compliance with regulatory standards.
The performance of weight detectors is a critical factor that directly impacts the overall efficiency of manufacturing processes. These devices are engineered to provide rapid and accurate results, even in high-speed production environments. With their ability to detect minute differences in weight, they ensure that each product is within the specified weight range, which is especially important in industries like food and beverage, where regulatory guidelines for weight accuracy are stringent.
Incorporating a weight detector into your production line not only improves product quality but also enhances operational efficiency. By automating the weight verification process, businesses can reduce the need for manual inspections, which can be time-consuming and prone to human error. Moreover, modern weight detectors are equipped with advanced features such as touchscreens for easy operation, real-time data analysis, and integration with other quality control systems, making them an invaluable tool for manufacturers looking to maintain high-quality standards while optimizing production throughput.
Overall, weight detectors are indispensable in modern manufacturing settings, providing precise, reliable, and efficient weight measurement solutions that contribute to better product quality, reduced costs, and enhanced customer satisfaction.
In today's fast-paced manufacturing environment, the need for accuracy and reliability in production lines has never been more crucial. Weight detectors are essential tools that play a significant role in ensuring product quality and consistency, particularly in industries such as food processing, pharmaceuticals, packaging, and more. These devices are designed to automatically measure the weight of products, checking for underweight or overweight items in real-time, ensuring that every product meets the required specifications.
A weight detector is commonly integrated into automated production lines to streamline the quality control process. These systems utilize highly sensitive sensors and advanced algorithms to detect any weight discrepancies with remarkable precision. By identifying deviations in product weight, the system helps to prevent product waste, minimize errors, and maintain compliance with regulatory standards.
The performance of weight detectors is a critical factor that directly impacts the overall efficiency of manufacturing processes. These devices are engineered to provide rapid and accurate results, even in high-speed production environments. With their ability to detect minute differences in weight, they ensure that each product is within the specified weight range, which is especially important in industries like food and beverage, where regulatory guidelines for weight accuracy are stringent.
Incorporating a weight detector into your production line not only improves product quality but also enhances operational efficiency. By automating the weight verification process, businesses can reduce the need for manual inspections, which can be time-consuming and prone to human error. Moreover, modern weight detectors are equipped with advanced features such as touchscreens for easy operation, real-time data analysis, and integration with other quality control systems, making them an invaluable tool for manufacturers looking to maintain high-quality standards while optimizing production throughput.
Overall, weight detectors are indispensable in modern manufacturing settings, providing precise, reliable, and efficient weight measurement solutions that contribute to better product quality, reduced costs, and enhanced customer satisfaction.
Applications:
1. Used for automatic weight detection, upper and lower limit discrimination or weight classification selection on various automated assembly lines and logistics transportation systems. It can also be used for detection of excess and missing parts after product packaging.
2. Widely used in online testing in pharmaceutical, food, toys, hardware, chemical and other industries.
3. In addition, it can directly replace manual weighing to improve production efficiency and weighing consistency and reliability.
1. Used for automatic weight detection, upper and lower limit discrimination or weight classification selection on various automated assembly lines and logistics transportation systems. It can also be used for detection of excess and missing parts after product packaging.
2. Widely used in online testing in pharmaceutical, food, toys, hardware, chemical and other industries.
3. In addition, it can directly replace manual weighing to improve production efficiency and weighing consistency and reliability.
Features:
1. Large color LCD touch screen interface, easy to operate and intuitive to display.
2. Supports customization of multiple languages, the default is Chinese and English.
3. It can be set to store 100 kinds of product detection data to facilitate users to switch and call.
4. Equipped with automatic photoelectric detection of empty packages, adjustable conveyor belt speed, and automatic learning function.
5. Parameter settings are password protected and can only be operated by managers.
6. Automatic zero-point tracking system to ensure reliable detection data.
7. The single-chip microcomputer system is independently developed and has a unique filtering algorithm to ensure system stability.
8. The mechanical structure is simple and the buckle-type conveyor belt is easy to disassemble, clean and maintain.
1. Large color LCD touch screen interface, easy to operate and intuitive to display.
2. Supports customization of multiple languages, the default is Chinese and English.
3. It can be set to store 100 kinds of product detection data to facilitate users to switch and call.
4. Equipped with automatic photoelectric detection of empty packages, adjustable conveyor belt speed, and automatic learning function.
5. Parameter settings are password protected and can only be operated by managers.
6. Automatic zero-point tracking system to ensure reliable detection data.
7. The single-chip microcomputer system is independently developed and has a unique filtering algorithm to ensure system stability.
8. The mechanical structure is simple and the buckle-type conveyor belt is easy to disassemble, clean and maintain.
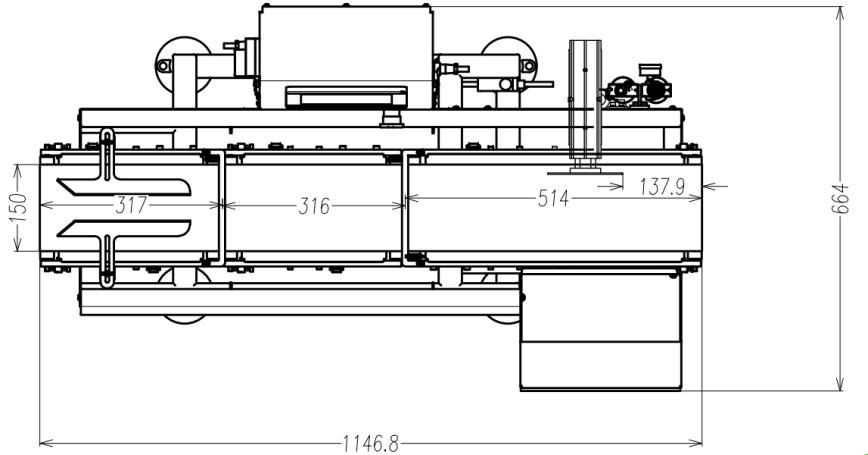
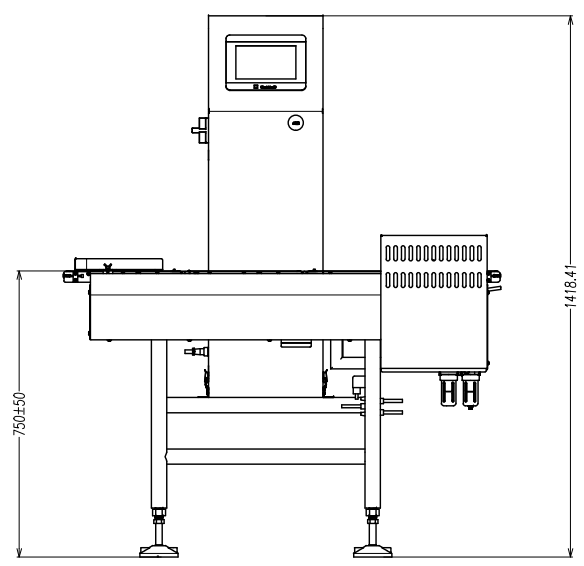
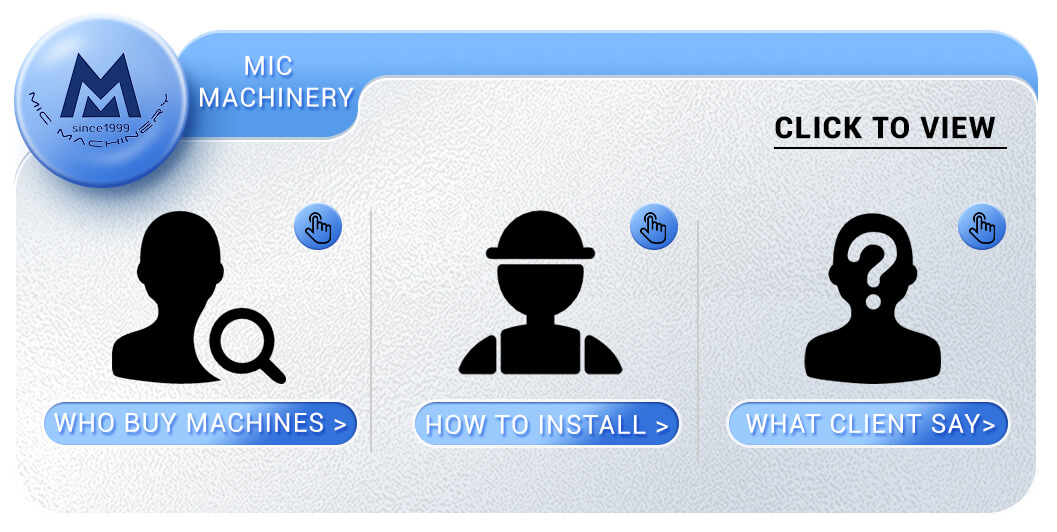