- Mobile: 0086-13083991987
- E-mail: market@micmachinery.com
- Shipment: exporting country
- Customer reviews: click on
Introduction:
In the world of wax-based craftsmanship, where warmth meets artistry, the Hot Wax Filling Machine emerges as a pivotal force, seamlessly blending technological precision with the creative process of candle making. This cutting-edge machine redefines the art of hot wax filling, offering artisans and manufacturers a powerful tool to bring their candle creations to life. By exploring its unique product characteristics, versatile applications, and the intricate mechanical principles guiding its operation, we unravel the essence of hot wax filling excellence. From boutique candle ateliers to industrial-scale production, the Hot Wax Filling Machine ensures each candle is infused with the warmth and precision synonymous with quality wax products.
Product Characteristics:
The Hot Wax Filling Machine showcases an array of exceptional characteristics meticulously engineered for precision and efficiency. Crafted from durable materials, often stainless steel, these machines ensure longevity while maintaining the highest standards of quality. Featuring advanced temperature controls and adjustable dosing systems, they cater to various candle sizes and shapes, allowing artisans to achieve the desired texture and finish for their creations. Intuitive interfaces enhance operational efficiency, providing users with control over the molten wax filling process. Equipped with anti-drip mechanisms and secure sealing, these machines preserve the integrity of the wax, delivering candles that captivate with their smooth finish and even burn.
Product Applications:
The applications of the Hot Wax Filling Machine span the entire spectrum of candle production, offering a versatile solution for both artisanal workshops and large-scale manufacturing facilities. Candle makers benefit from the precision of these machines, enabling them to efficiently produce batches of consistent and high-quality candles. Industrial-scale manufacturers leverage Hot Wax Filling Machines for bulk production, ensuring uniformity in size and shape across their product lines. Whether crafting traditional pillar candles, elegant taper candles, or intricate molded designs, these machines cater to the diverse needs of the candle industry, ensuring each creation is a testament to the art of hot wax filling.
Mechanical Principle:
At its core, the Hot Wax Filling Machine operates on advanced mechanical principles designed for precision and reliability in handling molten wax. Utilizing a dosing pump, conveyor systems, and filling nozzles, the machine accurately measures and dispenses the specified quantity of hot wax into individual molds. Temperature controls ensure the wax remains at the optimal temperature for filling, while integrated sensors and programmable logic controllers (PLCs) oversee the entire process. The precision of the machine guarantees even distribution, minimizing errors and enhancing the overall efficiency of the hot wax filling operation.
In conclusion, the Hot Wax Filling Machine stands as a symbol of craftsmanship and efficiency in the world of candle production. Its exceptional product characteristics, versatile applications, and advanced mechanical principles make it an indispensable asset for candle makers and manufacturers globally. Embracing cutting-edge technology, this machine not only ensures the precision of hot wax filling but also upholds the highest standards of quality and consistency. As a fundamental component in the creation of candles, it continues to shape the way wax products are crafted, ensuring each candle is a masterpiece of warmth, beauty, and precision.
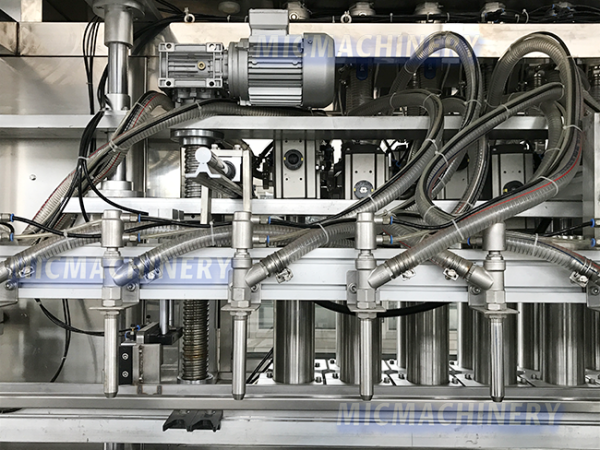
Filling head
The hot wax is put into the material cylinder, the piston to pump the hot wax into the measuring cylinder. Then the piston moves up to send the hot wax to the filling pipe. At the same time, when the bottle enters the filling machine through the conveyor belt, the filling head moves down to start filling. After filling, the conveyor belt will automatically send the bottle to the capping station.
(Filling process without drip leakage, the number of filling head can be customized according to your needs and diameter of filling head basis on the diameter of your barrel’s mouth)
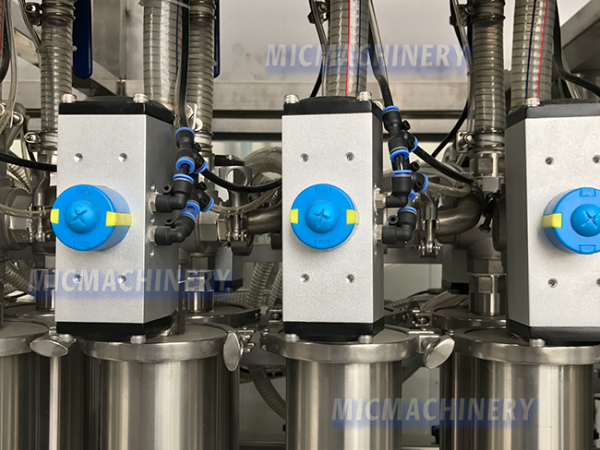
The three-way valve
The three-way valve is controlled by PLC system, The three-way valve rotates internally to adjust the connection between the material box and the measuring cylinder cylinder or the measuring cylinder cylinder and the filling pipe. Accordingly it controls the movement of materials from the material tank to the dosing cylinder and then to the filling pipe.
Main working process: downward movement of the piston to fill the material from the material cylinder to the measuring cylinder, and then controls the upward movement of the piston to send the material to the filling pipe and start filling
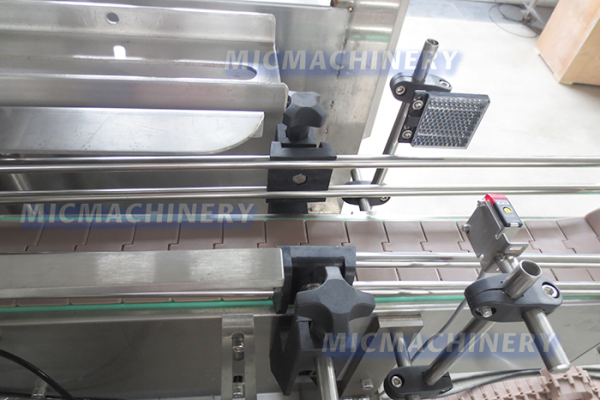
Conveyor belt
When the bottle is placed on it, the conveyor belt takes the bottle into the filling machine and starts filling. After filling, it is sent out through the conveyor belt. The whole process is convenient to save time .
This conveyor belt can be different size of bottle,The width between the two pipes can be adjusted according to your container,ensure smooth bottle safely from the conveyor belt moved.On the side of the conveyor is equipped with sensors that can automatically identify when the bottle to go out or, in order to send signals to filling station of screw cap.
This machine is suitable for filling a liquid and sauce cream products, especially for high viscosity materials, the effect is obvious.
1. Adopt PLC programmable control system with touch screen interface.
2. Automatic bottle feeding, automatic filling, automatic bottle.
3. Adopt servo motor drive, double screw-rod drive, Control the movement of the piston rod to ensure the stability of the filling.
4. Adopt double-ball screw rod filling the filling nozzle dive
5. It can be used with capping machine, labeling machine supporting the formation of the production line
6. It combines optical, mechanical, electrical, gas in one. It is easy to operate a filling machine.
7. Having a stable and reliable operation, high production efficiency, strong adaptability.
If you want to know more models of filling machine, you can refer to the table below:
Model |
MIC V01 |
MIC-ZF4 |
MIC-ZF6 |
MIC-ZF8 |
MIC-ZF12 |
MIC-ZF16 |
MIC-ZF20 |
Application |
High Viscosity Materials,Butter,Mayonnaise,Honey,Tomato Sauce,Cream , Liquid soap , oil product ,Lotion And So On |
||||||
Packing Type |
Metal Cans, jar, Glass Bottle , Bag, Plastic Bottle Etc |
||||||
Speed |
5-25 B/M |
192-220 B/h (basis on 25L) |
1300-1500 B/h (basis on100ml bottle) |
≤1800 B/h ( basis on 1000ml bottle) |
3000B/h (basis on 350ml) |
3200 B /h |
≤4000 B/h (basis on1L bottle) |
Filling Arrange |
10-20ML. 25-250ML. 50-1000ml, 50-500ML.100-1000ML.250-2500ML. 1000-5000ML 100ml-5L.(10ml-5l) |
||||||
Power |
30W |
3.0Kw |
2.8kw |
3kw |
2.8kw |
2Kw |
3.0Kw |
Size |
1000*480*700 mm |
2500*1600*2500 mm |
1840*1400*2500 mm |
2000*1400*2500 mm |
1600*1400*2300 mm
|
2440*1240*2350 mm |
2800 *1400*2500 mm |
Weight |
35 Kg |
700 kg |
600kg |
1000kg |
3000Kg |
700 kg |
1000 kg |
in short, we will try our best to provide you with satisfactory service,the following is our customer feedback.
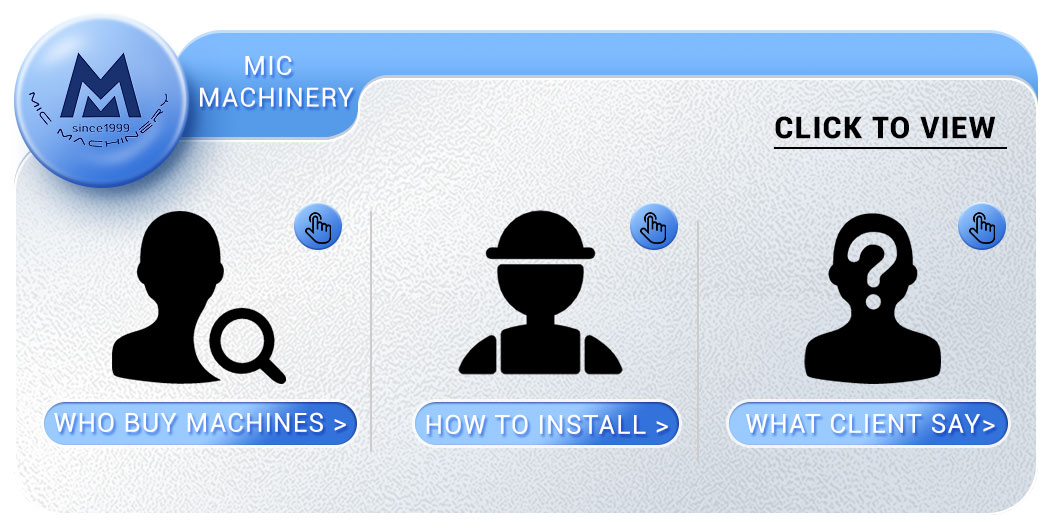