- Mobile: 0086-13083991987
- E-mail: market@micmachinery.com
- Shipment: exporting country
- Customer reviews: click on
In pharmaceutical manufacturing, the accuracy and efficiency of syrup packaging are crucial for maintaining product quality and meeting regulatory standards. The Syrup Packing Machine plays a pivotal role in this process, offering automated and precise packaging solutions for syrup products. Let's delve into its performance, focusing on its role as a syrup filling machine, automatic syrup filling machine, and its significance in pharmaceutical applications.
Maximizing Performance with Syrup Packing Machine
Precise Filling and Packaging: The Syrup Packing Machine ensures accurate and consistent filling and packaging of syrup products. Equipped with advanced dosing mechanisms and controls, it maintains uniform filling levels, critical for dosage accuracy and product integrity in pharmaceutical formulations.
Efficiency through Automation: Serving as an automatic syrup filling machine, this equipment streamlines the packaging process by automating dosage adjustments and bottle handling. Its high-speed operation and automated functionalities reduce human intervention, minimize errors, and increase production throughput, thereby optimizing efficiency in pharmaceutical manufacturing.
Versatile Packaging Solutions: Tailored for syrup products, the Syrup Packing Machine offers versatility in packaging options. Whether it's bottles, pouches, or other container types, this machine can accommodate various packaging formats, meeting diverse pharmaceutical packaging requirements.
Serving as a Syrup Filling Machine, Automatic Syrup Filling Machine, and its Role in Pharmaceutical Applications
Syrup Filling Machine: The Syrup Packing Machine acts as a specialized solution for filling and packaging syrup products accurately and efficiently. Its precise dosing mechanisms and automated controls ensure uniform filling and packaging, minimizing product wastage and maximizing dosage accuracy for pharmaceutical formulations.
Automatic Syrup Filling Machine: By automating dosage adjustments and packaging processes, this equipment enhances efficiency and productivity in syrup packaging operations. Its seamless integration into pharmaceutical production lines reduces labor costs and increases overall throughput, making it an indispensable asset for pharmaceutical manufacturers.
Syrup Filling Machine Pharmaceutical Applications: The Syrup Packing Machine plays a crucial role in pharmaceutical manufacturing, ensuring the consistent and precise packaging of medicinal syrups. With its adherence to pharmaceutical standards, it upholds product quality and regulatory compliance, safeguarding patient safety and trust in pharmaceutical products.
Conclusion
The Syrup Packing Machine represents a significant advancement in pharmaceutical packaging, offering precision, efficiency, and versatility. Whether serving as a syrup filling machine, automatic syrup filling machine, or supporting pharmaceutical applications, it plays a vital role in ensuring the quality and safety of medicinal syrups for patient consumption. By investing in this advanced equipment, pharmaceutical manufacturers can enhance efficiency, reduce costs, and uphold their commitment to delivering high-quality medicinal products to consumers.
The machine is combined with rinsing, filling and capping, which special designed for PET bottled. It is stable characteristic, advanced technology, nice appearance and complete function.
Technical structure feature:
A. Rinsing part:
☆ It is rotary type, mainly sued for rinsing new bottles send the bottles to the filling machine.
☆ Renew stainless steel clip, simple structure, convenient adjustment; small area touch with bottle mouth, avoid the secondary pollution for the bottle mouth efficiently.
☆ Bottle rinsing machine inlet pipe equipped with pressure gauge.
☆ Bottle rinsing machine equipped with water collector to callback rinsed water.
B . Sauce Filling part:
Sauce filling machine will play a role to fill the sauce products into the bottle; all the contact parts with the products are adopted stainless steel material and special materials, comply with food sanitary standard.
Filling valve is a key part of the machine, plunger-type ration filling valve is special used for filling solid state suspended substance products or high viscosity products. The valve is installed on the filling cylinder through positioning screw, pressure plate and pin position; the valve has two working positions: one is closed valve for the liquid inlet, with the function of opening and closing of valve idler wheel, the pilot valve drives operating loop running to the valve shut state, the valve nozzle is shut by operating loop, the plunger moves up with the drive of lifting idler wheel, the products in the filling cylinder is inhaled to the plunger valve cavity through the perforated hole of operating loop with cylinder; the other is filling with opening valve, with the function of opening and closing idler wheel, the operating shaft drives operating loop to opening valve state, the perforated hole of operating loop is closed, the plunger moves down with the drive of lifting idler wheel, the products in the plunger valve cavity are extruded, and filling to the container under the valve through perforated hole of operating loop; the adjustment of filling capacity will be achieved through the adjustment of elevator idler wheel, the valve of filling scope is 0~100ml; the contact parts with valve and products all adopt materials conform to the food sanitary requirements;
The machine adopts filling with no touch of bottle mouth.
C . Capping parts:
The capping rotates through reduction box drive rotational wheel, which make the cap leave the hopper with the function of centrifugal force. There is a separation device for right cap and reverse cap at the entrance, when the reverse cap passes, the cap automatically fall into and return to pipeline, and blow the reverse cap automatically to hopper through wind power. Only right cap could enter into skids smoothly, the volume of cap inside of hopper will be automatic inspected by electric switch to control cap conveyor, and that ensures best effect of cap down. When the right cap enters into the slide way, it could smoothly enter into cap feed plate, to prevent accidents, there is an anti reverse cap drive plate device to match with slide way, to ensure that the access to the cap feed plate is correct. The slide way is also equipped with a pair of photoelectric switch, when testing no cap, then an immediate halt to the host. In order to effectively remove non-anti-theft ring bad caps and cleanup additional caps in hopper, there is an active exit in front of the hopper exit can meet this function.
In short, we will try our best to provide you with satisfactory service,the following is our customer feedback.
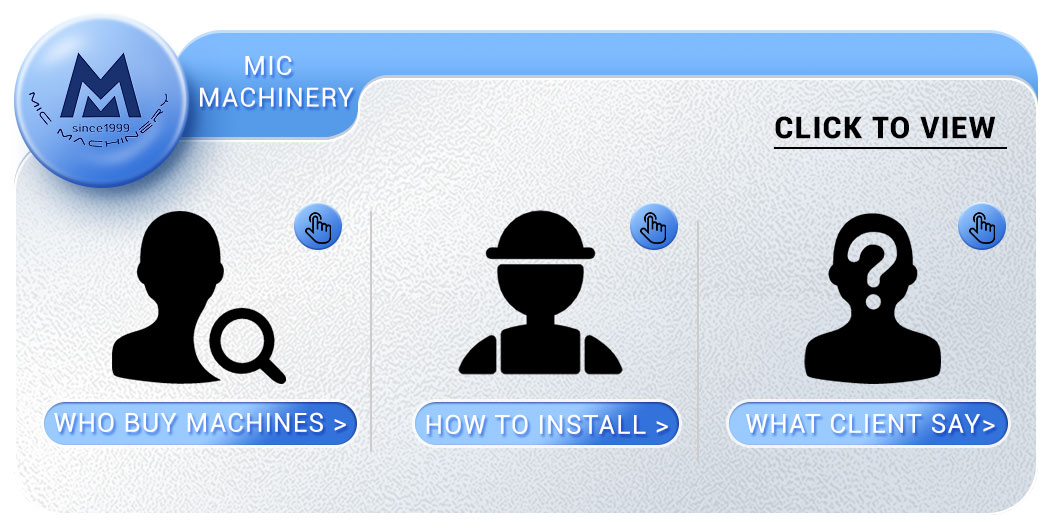
Production capacity |
12000bph |
Motor power |
0.37KW |
Compressed air consumption |
1m 3/min (0.6MPa) |
Overall dimension |
L*W*H (600mm*800mm*2800mm) |
Weight |
200KG |
Components |
Standard Components |
Touch screen |
SIEMENS (Germany) / MITSUBISHI (JAPAN) |
PLC |
SIEMENS (Germany) / MITSUBISHI (JAPAN) |
Inverter |
MITSUBISHI (JAPAN)/Danfoss(Denmark) |
Contactor |
SCHNEIDER (France) |
Breaker |
SCHNEIDER (France) |
Air switch |
SCHNEIDER (France) |
Pneumatic components |
CAMOZZI (Italy)/SMC(Japan) |
Photocell switch |
SICK/TURCK (Germany)/OMRON/KEYENCE(Japan) |
Proximity switch |
SICK/TURCK (Germany)/OMRON/KEYENCE(Japan) |
- MIC Sterile Syrup Filling Machines ( 30-200 Bottles/Min )
- MIC Four Heads Syrup Filling Machine Pharmaceutical (30-80 Bottles/Min)
- MIC High-Speed Syrup Bottle Filling Machine (16 Heads 30-450 Bottles/min)
- MIC 12 Heads High Speed Syrup Filling Machine (10000Bottles/H)
- MIC Six Heads Syrup Bottle Filling Machine
- MIC Syrup Filling Machine Pharmaceutical (200Bottles/m)
- MIC Automatic Syrup Filling Machine (30-50Bottles/m)
- Rotary thick syrup Filling Machine
- MIC-LL45 Syrup Filling Machine (20-40Bottles/m)