- Mobile: 0086-13083991987
- E-mail: market@micmachinery.com
- Shipment: exporting country
- Customer reviews: click on
The aseptic filling production line for eye drops is composed of six main parts: bottle arrangement, transportation, aseptic purification gas washing bottle, filling, inner stopper and outer cap. It is mainly used to complete the bottle arrangement, bottle transportation, gas washing, metering and sub packing, stopper, capping and capping of eye drops bottle. The whole production process is completed under 100 level laminar flow protection and aseptic isolation operation, The production line is also suitable for the production of other small capacity plastic bottles.
*Automatic bottle handling system
*Conveying bottle, removing bottle pouring system
*Static elimination, air washing bottle system (optional)
*Static electricity elimination, gas washing plug cap system
*Precision ceramics, filling and bottle dividing system (optional)
*Vacuum plug system
*Grab and cover system
*Constant magnetic torque, positioning and capping system
*100 level laminar flow protection aseptic system
A vial packing machine is a specialized piece of equipment designed to efficiently and accurately pack vials into various types of packaging, such as blister packs, cartons, or trays. It is commonly used in the pharmaceutical, biotech, and healthcare industries to streamline the packaging process and ensure product safety and integrity.
The vial packing machine automates the packaging process, significantly reducing manual labor and increasing production efficiency. It can handle vials of different sizes and shapes, accommodating the specific needs of each product.
The machine operates by receiving vials from a feeding system, which can include a conveyor or other automated mechanisms. The vials are then guided into the packaging material, such as blister pockets or carton slots. The machine ensures precise placement of the vials, maintaining consistency and alignment throughout the packing process.
Advanced vial packing machines can also incorporate additional functionalities, such as labeling, leaflet insertion, and serialization. These features enhance product traceability, comply with regulatory requirements, and provide valuable information to end-users.
The benefits of using a vial packing machine include increased productivity, reduced labor costs, improved packaging accuracy, and enhanced product presentation. Moreover, the machine contributes to the overall safety and quality of the packaged vials, minimizing the risk of contamination and tampering.
In summary, a vial packing machine is a vital component in the pharmaceutical and healthcare industries, providing an efficient and reliable solution for packing vials into various types of packaging. Its automation capabilities and customizable features make it an essential tool for streamlining the packaging process and ensuring the integrity and safety of vial-based products.
Basic performance characteristics
1. Touch screen operation platform
2. Host frequency control, automatically display the current working frequency
3. The filling volume can be adjusted as a whole or fine-tuning
4. No bottle, no filling
5. If there is no bottle, there is no plug
6. No inner plug, no outer cover
7. The capping station is equipped with bottle clamping device and top cover device
eight Stop the machine when there is no bottle and start automatically when there is bottle nine When the rotary table clamps the bottle, the torque limiting device can stop the machine for protection
ten Equipped with a 60L liquid storage tank, two proximity switches on and off the floating ball in the liquid storage tank + angle valve control for automatic material replenishment (the liquid replenishment system of the liquid storage tank needs to be in the state of liquid replenishment when the main engine power is turned on, and after the power is turned off, the liquid replenishment system needs to be in the state of closed no matter how much the liquid level is)
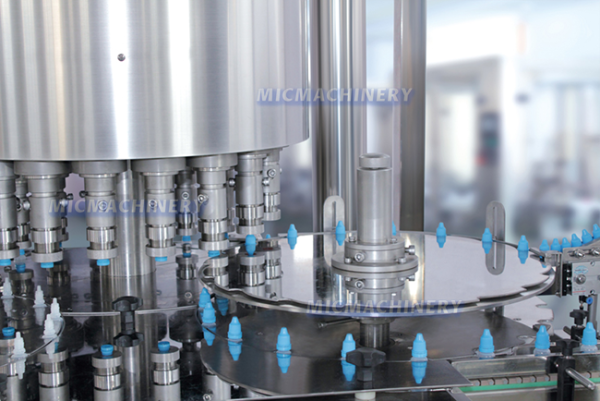
Plastic cap screwing system
The motor transmits the power to the main shaft through the transmission device, so that the turntable rotates. Because the central gear does not rotate, the rotary cap rotates because of the rotation of the gear of the rotary cap shaft. The machine will automatically grab the cap, and the bottle will automatically screw the cap when it reaches the specified position,no bottle then no cover, when the rotation of the cap side moving down, rotation (pressure) cap under the action of the CAM to complete cover. Then by the drawing wheel into bottle delivery.
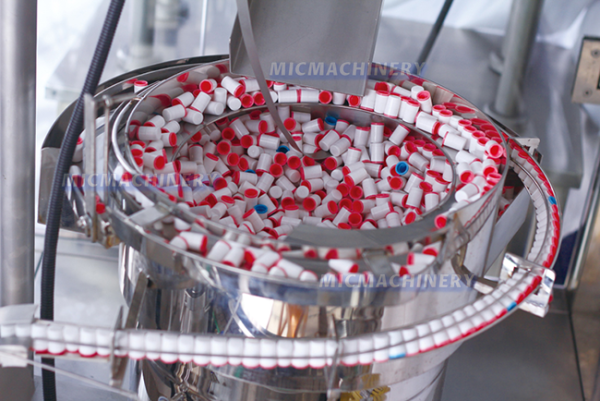
Cover loading automatically
Cover feeding cage with vibrating disk is connected to a pipe that carries the outside cover ,They automatically arranges the outside cover and deliver the outside cover.
In this way, the small bottle is covered in a Coherent process, reducing the manual contact with the syringe process, and ensuring bottle hygiene,At the same time, labor costs are reduced.
In short, we will try our best to provide you with satisfactory service,the following is our customer feedback:
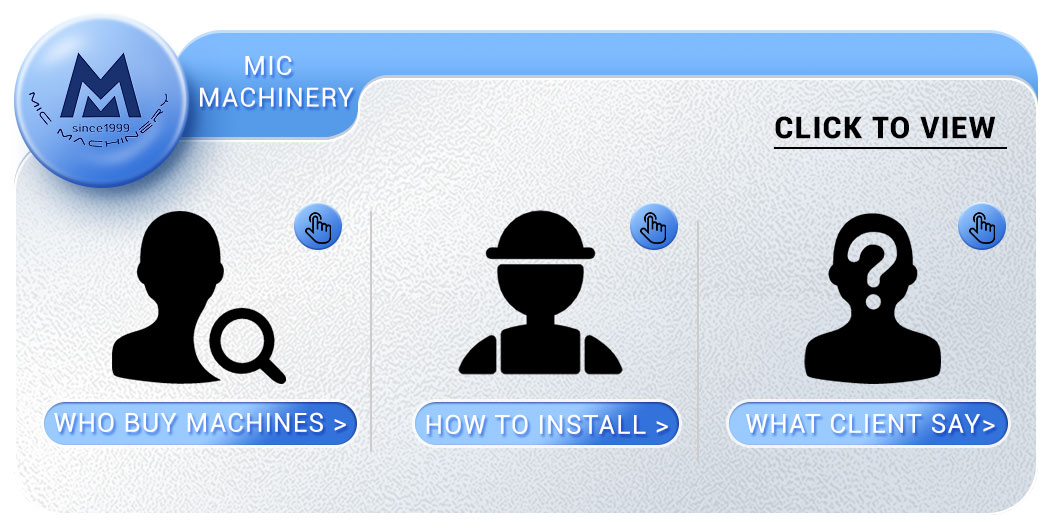