The Ultimate Guide to Silicone Filling Machines: Precision, Innovation, and Versatility
Whether you're packaging silicone for the construction, electronics, or automotive industry, having a reliable Silicone Filling Machine is essential for maintaining quality, efficiency, and hygiene standards.
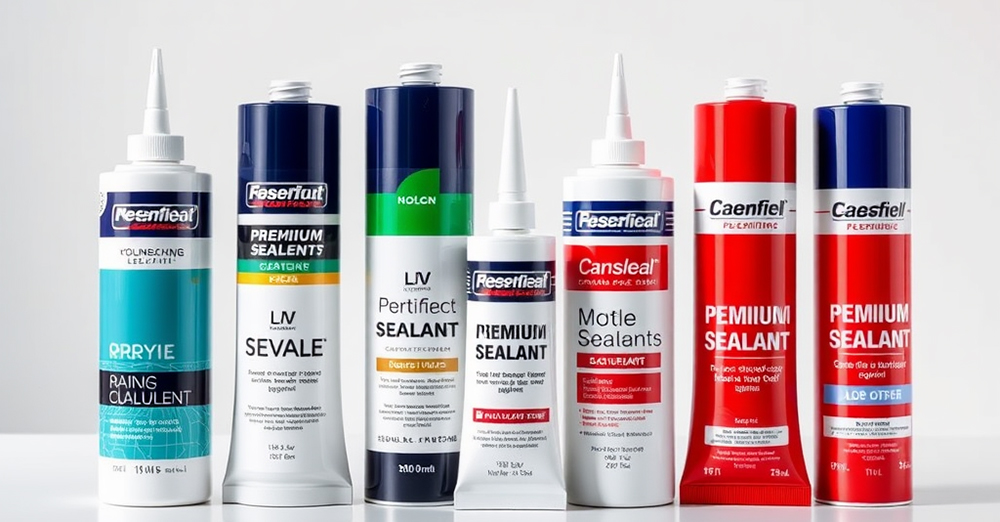
Silicone comes in many forms—cartridges, plastic tubes, dual-barrel packs—and each requires a machine built for the task. Let’s explore the most common types of machines available today:

1. Single Barrel Silicone Filling Machine
This type is ideal for standard cartridge filling. The single barrel Silicone Filling Machine uses a pneumatic system to fill sealant into 280ml or 300ml cartridges. These machines are typically compact, user-friendly, and designed for small to medium production runs.
Key features include:◆ Adjustable filling volume
◆ Anti-drip nozzles
◆ Quick-release clamps for cartridge holders
2. Double Barrel Silicone Filling Machine
Also known as a dual-component filling machine, the double barrel Silicone Filling Machine is designed for two-part silicone sealants, where resin and hardener must be filled separately but simultaneously. It ensures balanced mixing by delivering two materials into dual-chamber cartridges at a 1:1 or 10:1 ratio.
Applications:
◆ Industrial adhesives
◆ Structural silicone sealants
◆ Two-component epoxy resins

The automatic version is ideal for high-speed production environments. These machines feature a fully automated process from cartridge feeding and filling to capping and labeling. They often integrate PLC touch screen control, servo systems, and safety sensors.
Benefits:
◆ Labor-saving operation
◆ Consistent filling accuracy
◆ Supports integration with other production lines
4. Semi-Automatic Silicone Filling Machine
Designed for manufacturers who want control over the filling process, semi-automatic Silicone Filling Machines offer a balance of efficiency and flexibility. Operators load and unload cartridges manually, but filling is pneumatically driven and precisely regulated.
Advantages:
◆ Lower investment cost
◆ Easy to maintain and operate
◆ Suitable for various product viscosities
5. Silicone Cartridge Filling Machine for Sausage and Caulking Tubes
Beyond cartridges, the market increasingly demands machines that fill plastic tube filling formats such as sausage packs or caulking-style soft tubes. These packaging types are economical, space-efficient, and increasingly popular in global markets.Special features include:
◆ Compatibility with aluminum or laminated tubes
◆ Sealing by ultrasonic or heat sealing
◆ Multiple filling heads for higher output
Modern silicone filling machines are not limited to a single packaging type. Depending on the industry, machines are often compatible with:
◈ Plastic tubes
◈ PE or laminated soft tubes
◈ Aluminum foil cartridges
◈ Paperboard sausage film packs
◈ Coaxial dual tubes for dual-component adhesives
This versatility makes silicone filling equipment suitable for various applications, from bathroom sealants to LED potting compounds and fireproof insulation materials.
Key Features That Matter
Here’s what manufacturers look for in a modern Silicone Filling Machine:1. High Filling Accuracy
Volumetric or weight-based filling systems ensure each cartridge or tube receives the exact amount of product—critical for maintaining product integrity and cost-efficiency.
2. Easy Product Changeover
The ability to switch between different silicone viscosities and cartridge sizes quickly improves production flexibility and reduces downtime.
3. Anti-Drip Technology
Silicone is messy—anti-drip nozzles prevent product from leaking after filling, reducing waste and maintaining a clean production environment.
4. Durable Materials
Most machines are constructed from stainless steel and PTFE-coated components to resist corrosion and improve longevity.
5. Optional Heating Functions
For high-viscosity silicone, heating jackets or thermostatic controls can be added to maintain flowability.
Customization and Integration
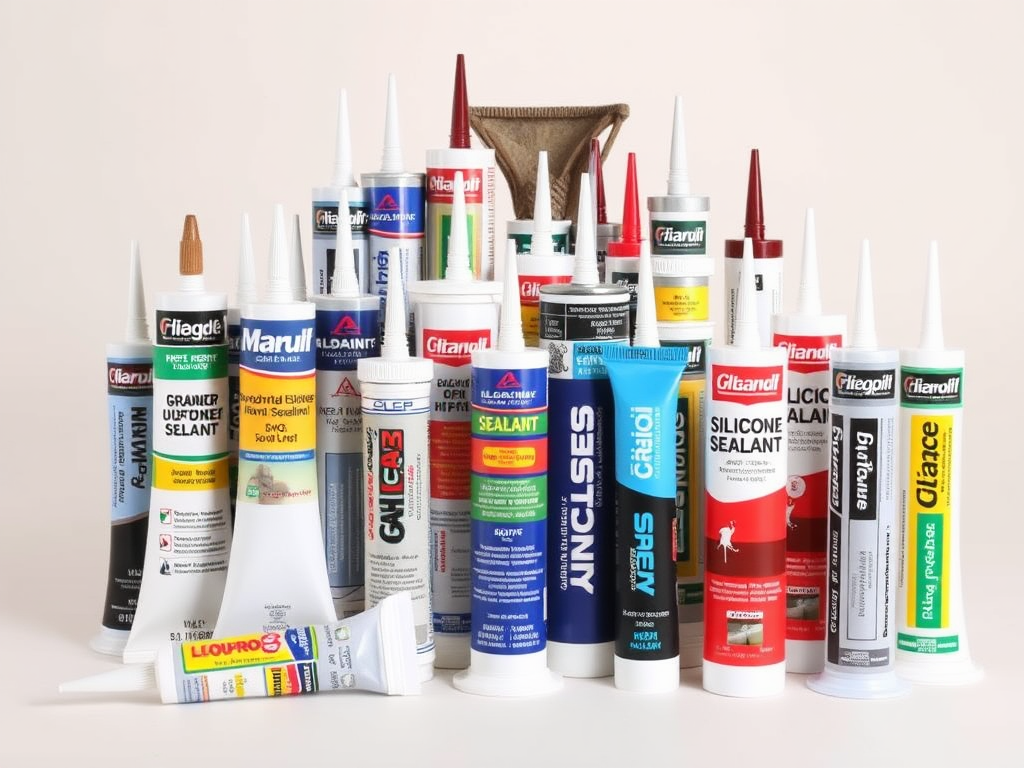
Most professional suppliers, like Mic Machinery, offer customization options:
◈ Custom filling nozzles◈ Extra filling heads
◈ Vacuum de-aeration systems for bubble-free filling
◈ Hopper heaters
◈ Capping and labeling modules
These upgrades allow seamless integration with other machines in your production line, improving efficiency from filling to final packaging.
Silicone can harden and clog components if left unattended. That’s why proper maintenance is crucial:
◈ Use quick-cleaning valves and hoses
◈ Perform regular pneumatic and pressure checks
◈ Lubricate moving parts monthly
◈ Replace O-rings and gaskets periodically
Well-maintained machines not only perform better but last longer and reduce operational costs.
Mic Machinery: Your Trusted Partner
Mic Machinery has years of experience in designing and manufacturing silicone tube filling machine solutions tailored for global clients. Our products are built for:
◈ Efficiency
◈ Durability
◈ Flexibility
◈ Hygiene compliance
From standard configurations to fully customized machines, we support your operation with expert consultation, installation, and after-sales service.
Model |
|||||||||
Filling Volume Range |
3-30ml/30-75ml/75-150ml |
3-20ml, 15-75ml, 75-250ml |
Max 310ml |
Max 600ml |
100-300ml |
280-380ml (customizable up to 400-600ml) |
200-600ml (customizable) |
100-300ml |
300-310ml |
Production Speed |
30-75 Tubes/min |
40-45 Tubes/min |
40-60 Cartridges/min |
10-25 Pieces/min |
10-30 Bottles/min |
15-23 Cartridges/min |
15-23 Cartridges/min |
10-30 Bottles/min |
20-30 Cartridges/min |
Power |
2.2Kw |
2.2Kw |
- |
- |
- |
5.5Kw |
5.5Kw |
- |
1.5Kw |
Air Pressure |
- |
- |
≮0.5MPa |
0.6-0.8 MPa |
0.4-0.8Mpa |
0.55Mpa-0.65Mpa |
0.55Mpa-0.65Mpa |
0.4-0.8Mpa |
0.6 Mpa |
Weight |
850Kg |
800 Kg |
1100Kg |
650Kg |
550kg |
700 kg |
700 kg |
550kg |
300Kg |
Dimension (L×W×H) |
1950×800×1850mm |
1950×800×1850mm |
5200×1450×2200mm |
1950×1150×1950mm |
1200×1000×1800mm |
1200×900×1800mm |
1200×900×1800mm |
1200×1000×1800mm |
1000×800×1650mm |
Suitable Container |
Aluminum Tube |
- |
¢50mm×300ML |
¢44mm/¢46mm/¢48mm |
- |
Ф10mm-Ф150mm (customizable) |
Ф10mm-Ф150mm (customizable) |
- |
300-310ml cartridge |
Applications |
Silicone,Ointment, Cosmetic |
Silicone,Toothpaste, AB Glue |
Silicone |
Silicone |
Silicone |
Silicone |
Silicone Sealant |
- |
PU glue, Silicone Sealant |
Global Trends in Silicone Packaging
Today’s packaging trends are evolving toward:
◈ Eco-friendly packaging formats like laminated and recyclable tubes
◈ Smart automation to reduce human error and downtime
◈ Digital traceability via QR or laser coding for quality control
◈ Compact and portable sealing for mobile repair kits
These shifts highlight the importance of investing in adaptable and forward-thinking equipment.
Ready to upgrade your filling line?
Get in touch with Mic Machinery’s technical team for expert consultation and customized solutions built to meet your unique production goals.